Hitit Seramik keeps working for a more livable future through its sustainability policies.
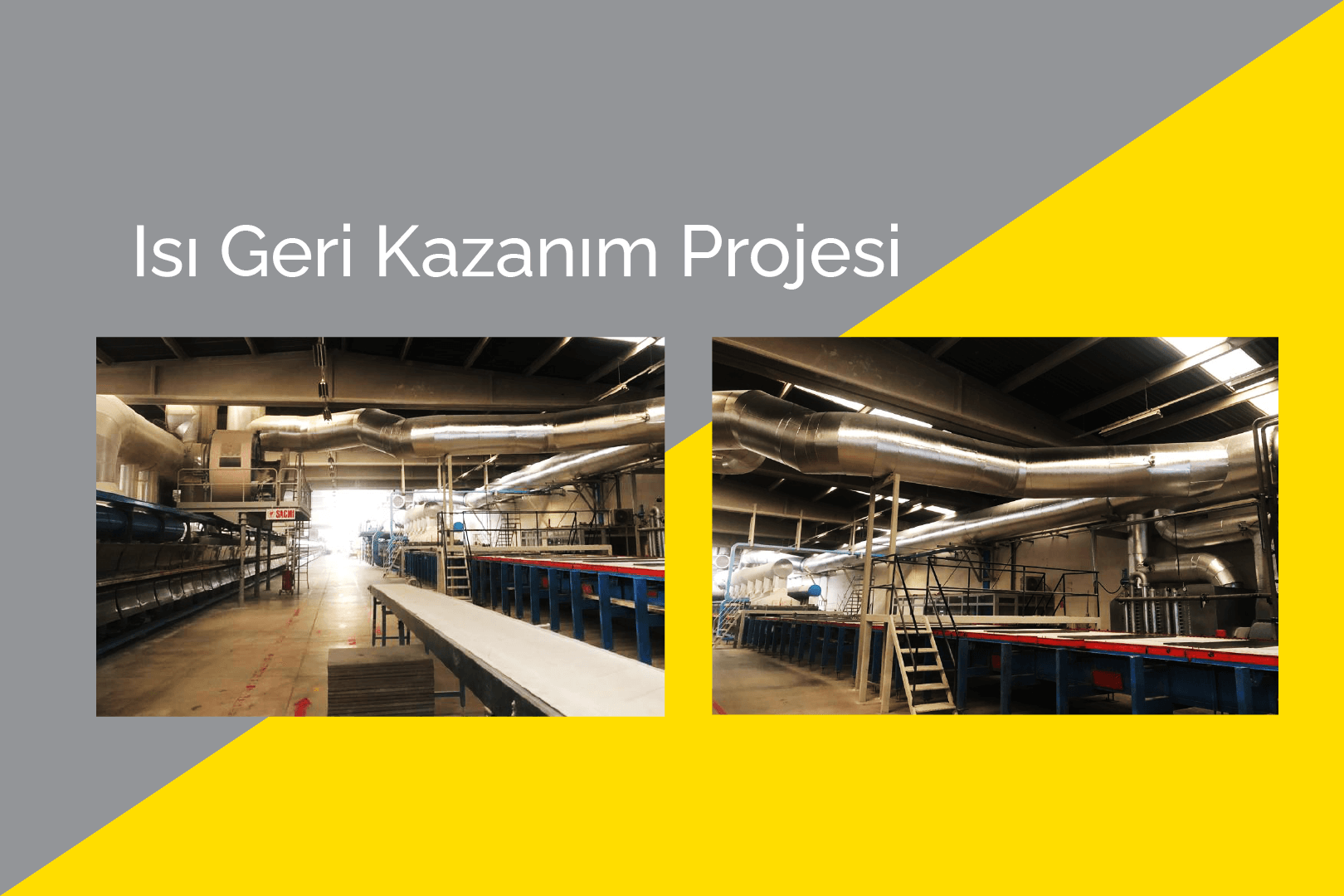
HEAT RECOVERY PROJECT
The recent increase in the energy unit prices in global markets has become a major competitive element in terms of costs for particularly the ceramic industry that has energy-driven processes. Particularly, as one of the key inputs of production covering approximately 60% of industrial costs alone, energy is one of the main considerations for manufacturers. As already known, the production phases of ceramic coating materials have a mode of production that includes heat-intensive processes such as drying-firing and space heating. The main source of energy for these processes is thermal energy which is mainly derived from natural gas. Moreover, the energy required for satisfying the comfort of employees, heating their indoor/outdoor spaces, and meeting their hot water needs is also obtained from natural gas. It is well known how greatly the consumption of fossil fuels such as coal, oil, and natural gas contributes to the climate change which has been felt globally due to environmental pollution in recent years. Air pollution, which has been intensely observed due to especially the carbon emissions, requires organizations to consider their use of energy sources in terms of not only costs, but also environmental protection awareness. Hitit Seramik acts with the mission of sustainability in environmental scale as well as capacity, quality, cost, and production matters. Within this mission,
-
- Energy conservation
- Energy efficiency
are the highlights. Especially the “waste heat recovery project” has been included in the scope of energy conservation.
In the functioning of this project;
-
- A total saving of around 20% has been achieved on the natural gas by the utilization of exhaust gases, obtained from furnaces, to use in another thermal process.
- Hot water has been produced by using the exhaust gases obtained from furnaces again, and the need for heat has been fulfilled by using this water in the building heating; also, the need for hot water has been fulfilled by heating the mains water for daily use.
- The production lines in the process have been heated through hot air to satisfy the comfort of employees.
- With 20% saving on natural gas, the environmental damage has been minimized through the prevention of natural gas-based carbon emissions.
- The aim has been to contribute to the national economy in connection with the reduction of natural gas consumption in production process.
- The company has earned its place as one of the leading brands in adopting a green policy by reducing the carbon footprint (Life Cycle Assessment), i.e. carbon emissions, in ceramic production below the international standards.